Scarsdale – Tudor
A 1920’s English Tudor with an elegant distribution on both the first and second floor was gutted inside and out, re-designed, enlarged and re-built to a master-builder standard using traditional materials and uncommon workmanship. The excellent location and beautiful original structure fed the builder’s passion for the project and resulted in the use of many long-lasting materials and expensive features not all of which meet the eye. The result is a warm traditional house, new from the framing out that has extremely low maintenance. Progress photos can be seen by clicking on the links above: outside, inside, framing, and mechanicals.
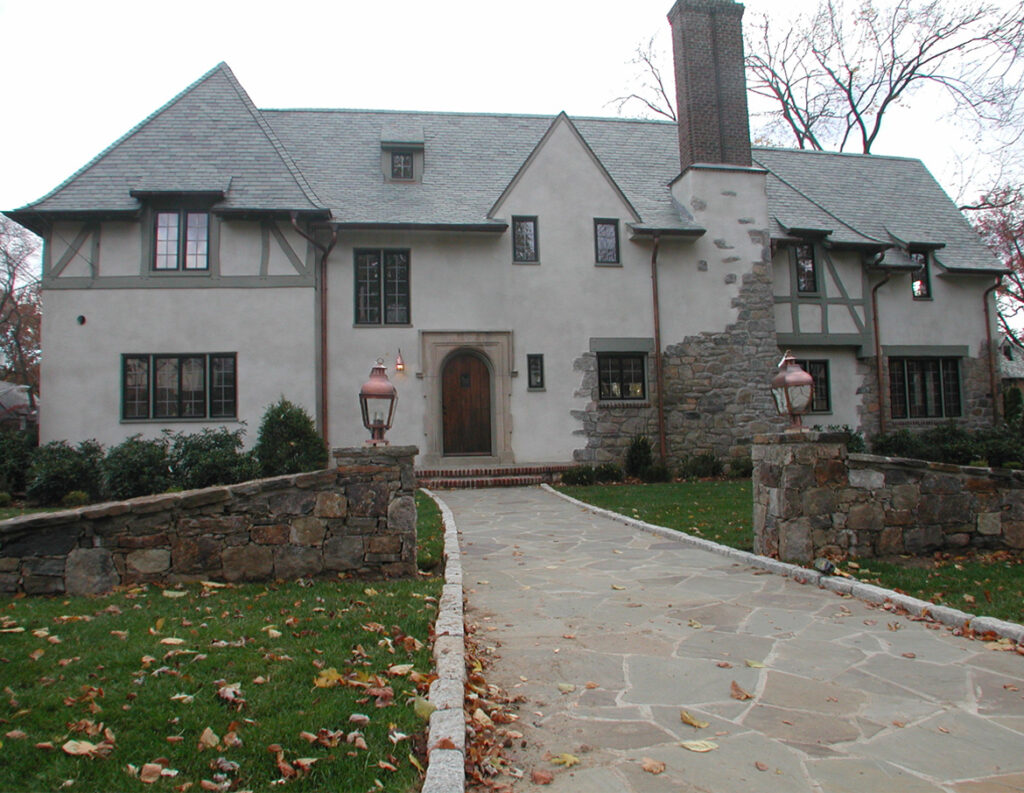